Beter Wonen: Working smarter, doing better with Lean
Beter Wonen Vechtdal manages approximately 3,500 rental homes in Hardenberg and the surrounding area. The goal of Beter Wonen Vechtdal is to offer affordable housing in livable neighborhoods. About 35 people work within the organization, divided into various departments. Beter Wonen has defined its desired image in the core values: Close, Together, The Conversation.
Want to know more?
Symbol has extensive experience with Lean implementations at housing associations. Call us for other references or make a no-obligation appointment by calling 053 – 20 30 240 or using the form below!
We spoke with Cees Naberman, deputy director of Beter Wonen Vechtdal. “We had been working in the same pattern for our main processes for several years. Until we decided to do more with fewer resources. In other words, work smarter. But how do you tackle that? Through a relation we ended up with a Symbol consultant. Our relation was very pleased with the approach and way of working.”
Systematic and structured work
“We had a clear mission statement and wanted to work there in a systematic and structured way. We have a number of young people in the organization who are together in an enthusiastic J-team (Youth Team). We asked them to come up with suggestions for improvement. Initially, the Symbol consultant introduced the Lean philosophy to this J-team. They are excellent at taking a fresh look at the organization, speaking a new language and putting on a different set of glasses. We really liked the approach of the Symbol consultant. Because of the good examples, you also see immediately that it works. The J-team has now been renamed V-team (improvement housing team).
The customized logo of the Improvement Housing Team
As MT, we identified which process we wanted to scrutinize first. That was equally our most important and difficult process, namely the rental mutation process. We started by training the J-team as Lean Facilitators so that they could make process improvements independently in the future. We also invited a fellow housing association through the Symbol consultant, to hear from them how they have implemented Lean in their organization. That was very interesting and inspiring.”
The ‘Yellow Cord Consultation’
“We went to Scania Production in Zwolle. Besides the whole Lean approach in the organization, the yellow cord with which the whole production can be stopped really appealed to us there. We came back inspired and immediately replaced our departmental meetings with the ‘yellow cord’ meeting. This is a daily morning meeting that we conduct standing with the themes, ‘What happened yesterday that we need to know and what are we going to run into today that we need to talk about.'”
A much more efficient mutation process
“Our rental brokerage process had been done the same way for many years. We were facing excessive vacancy costs. In part, this was caused by the process taking longer than the month’s notice. Measurements showed that the process took about 35 to 37 days. This led to vacancy. In a so-called brown paper session, we mapped out the Current State. This provided much insight into the process. There appeared to be a lot of carryover in the processes that slowed down. There was a lot of time between publication of the property and when it was completed. We then mapped out where we want to go (Future State) and where we could and should be more efficient.
With the insights gained in the brown paper sessions, a number of steps turned out to be redundant in our process. Waste, in other words. We deleted these immediately. For example, when someone terminated the lease, we always scheduled a visit with this person to tell them what to do. An initial inspection. And then at the end of the month followed the check to see if it had succeeded. In almost all cases, the house was in order and nothing more needed to be done. Then we went to the house with the new resident. We have now eliminated the final inspection. That has been a substantial savings.
We also redesigned the publishing process. Previously, we invited an average of 2 people to a viewing and accompanied them. Now we let people take care of that themselves. They themselves make the appointment with the current residents to visit. We actually had no added value here. In other words, the things we couldn’t actually contribute anything to we deleted. We started making policy on the rule rather than (as in the past) on the exceptions when reformulating and tightening the process steps.
These were the “quick wins” that could be implemented right away. We are now deepening. Namely, moving from paper to digital. Everything went by letter and work recorded in the house had to be re-entered and retyped internally. That’s duplication of effort. Soon our employees will go into the home with an iPad. Internally, however, the automation effort has yet to be made. By e-mail or through a website application instead of by letter. By the way, we do offer our tenants a choice in this. For example, older tenants find it more comfortable to continue working through paper. We want to make this turnaround this year.
By the way, we also made some minor improvements on 5S. For example, our printer rooms are now conveniently arranged. No one misses out on the stapler anymore and paper is always at the ready. No more annoyances or time spent searching.”
More conscious and entrepreneurial
“All in all, it gave us a lot. In addition to realizing considerable savings and thus achieving our goals, we also learned to look beyond our departments. We learned to think in a chain, constantly asking ourselves if the action adds value in the chain. We work better together and are more customer-oriented rather than departmental-oriented. Furthermore, we started to manage based on concrete information. We had no idea how long a process took. Now we measure and monitor that. We are no longer surprised by reports that suddenly confronted us with excessive vacancy rates.
Employees have also become more aware and entrepreneurial. As mentioned, there is thinking in the chain and, in doing so, in opportunities for improvement. No more “that’s the way things are done around here. We had initially trained 5 people as Lean Facilitators. With today’s knowledge, we believe that this number may be smaller per lean job. A smaller, coordinating team with cart leaders makes you more decisive and that increases speed.
Everything is definitively different
“What was a real eye opener for me is the art of getting rid of old patterns. You have to organize that and then do it. And then take small steps. That’s when the success rate is highest. Definitions and objectives must be absolutely clear. It cannot be that different people have different interpretations of it. Preparation is very important. Symbol’s consultant kept us on our toes in this regard.
We continue on the path we have taken. No way back either. The maintenance process and invoice processing, for example, are things we want to address. Yes, we have actually changed. We went through a fun and educational process that actually paid off. Your way of thinking has changed forever. In everything, even in everyday life you subconsciously think, could this be better, smarter, more efficient…. My motto? Lean works at Beter Wonen. No, Lean works everywhere: think smarter; do smarter!”
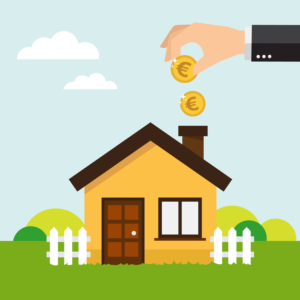
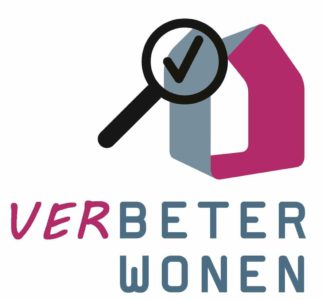