Training
Ontwikkel je kennis op het gebied van Operational Excellence, Continu Verbeteren, Problem Solving.
Consultancy
Wij helpen organisaties hun productiviteit te verhogen en bij het oplossen van complexe problemen.
Events
Blijf op de hoogte van de nieuwste ontwikkelingen en deel ervaringen met anderen.
Blijvende impact
20% – 60%
reductie van doorlooptijden
25.000+
mensen gecertificeerd in Lean Six Sigma
50%
halvering van interne afkeur en klantklachten
500+
organisaties op een hoger niveau gebracht
100+
ISO9001 en IATF16949 trajecten begeleid
Wat relaties zeggen
Lean Six Sigma training & certificering
Wij werken voor onze Lean Six Sigma opleidingen nauw samen met LSSA. Hierdoor kunnen onze trainingen worden afgesloten met een internationaal erkend certificaat.
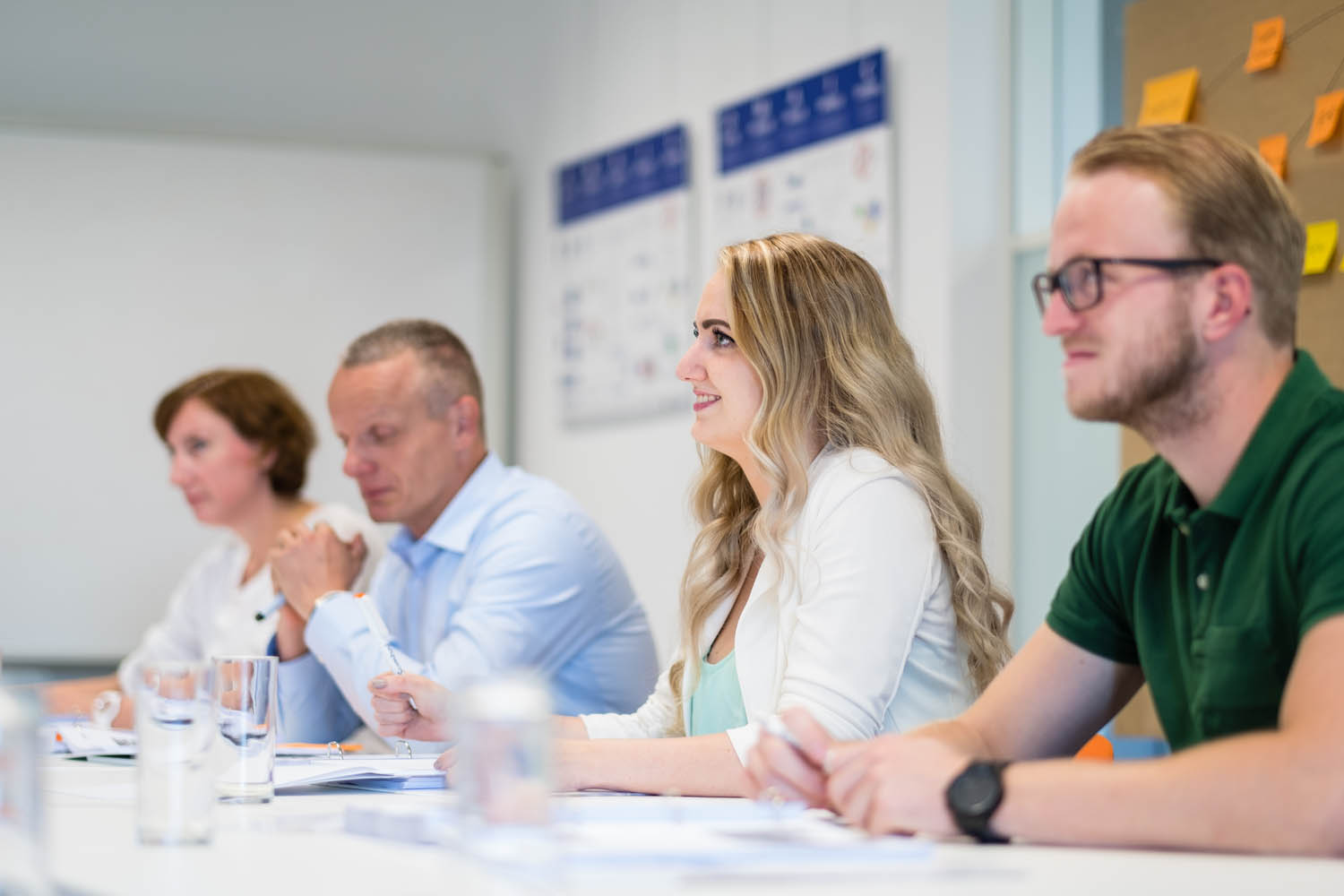
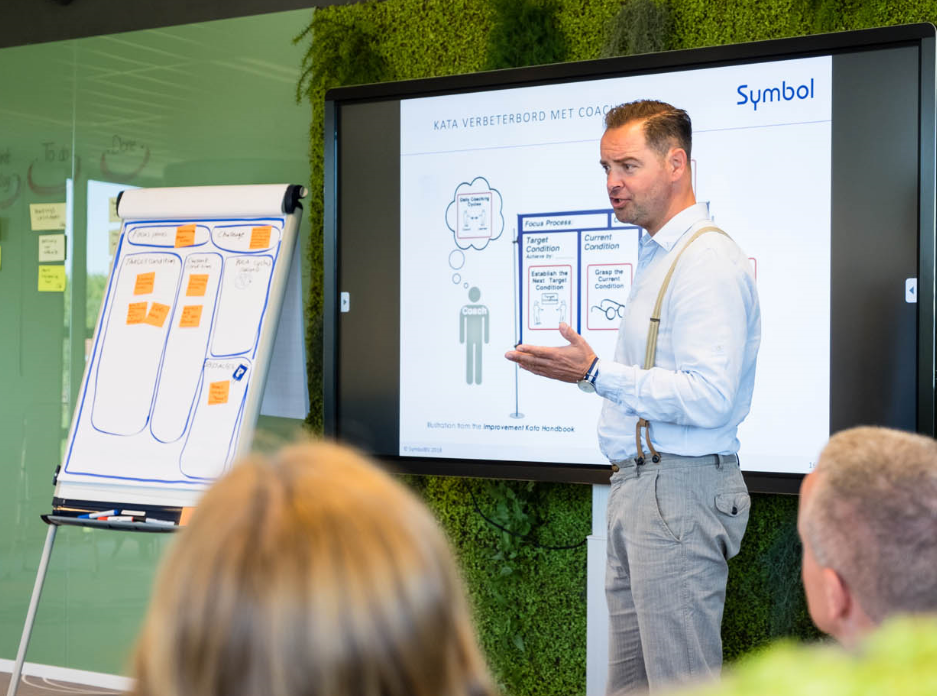
Transformatie dankzij Lean Six Sigma
Lean richt zich op het creëren van maximale waarde voor de klant, door met name verspilling te elimineren. Six Sigma richt zich op het verminderen van fouten door de variatie te reduceren. Hiervoor worden ook statistische methodieken ingezet. In onze Lean Six Sigma trainingen leer je methodieken uit beide elementen kennen en toe te passen. Maar wat is nu zo’n transformatie?
Lean Transformatieproces
Verbeter je organisatie naar een volgend volwassenheidsniveau
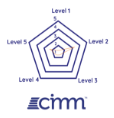
Assessment
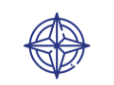
True North
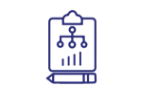
Plan van aanpak
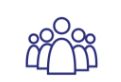
Teams
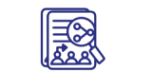
Project Charters
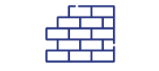
CIMM building blocks
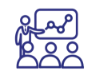
Training
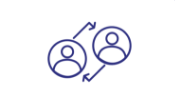
Coaching & Intervisie
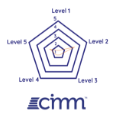
Assessment
Lean Six Sigma
Yellow Belt
Lean Six Sigma
Orange Belt
Lean Six Sigma
Green Belt
Lean Six Sigma
Black Belt