Municipality of Wierden: You don’t have to be sick to get better
The residents of the Twente municipality of Wierden can rub their hands together, because they live in “the best municipality in Overijssel. This is according to research by weekly magazine Elsevier and agency Louter, published in mid-2017. Wierden finished 21st nationally in this ranking, for which a total of 388 municipalities were surveyed. Still, according to the municipality of Wierden, there is always room for improvement. Hence, in late 2016, the municipality engaged Symbol to implement Lean in the organization.
Municipal Secretary Bjørn van den Brink explains, “2.5 years ago we started setting up an organizational development plan and, using our Demand-oriented Product Catalog, we also inventoried which processes we as a municipality were all dealing with. What turned out: we had many more processes than products. That’s how the question of Lean arose for us, because: were our processes really designed as efficiently as possible?” Van den Brink then invited three different agencies to interview. With Symbol’s consultants, it clicked right away. “That click was also the deciding factor. You enter into a long-term cooperation with each other, so that you understand each other and that you enjoy dealing with each other is very important.” Continue reading below.
Doing before, participating, doing yourself
Symbol started the process with a baseline measurement and training 12 volunteers to become Lean Grean Belts. The MT was also trained because Lean leadership is significantly different from traditional management. “Our principle is demonstrate, participate, do it yourself. We train process improvers, take management by the hand and set a good example, with the end goal that the organization can do it itself,” says Senior Consultant Jeroen Bos. “It is very important for the management team to support process improvers, since one of the things they have to deal with are people who find it exciting to change. It is also important that employees are given the space to work with process improvement. Any change takes time, especially in the beginning. Often that time is not there, or not made available. Employees are mostly busy doing their jobs as well as possible. When the MT encourages, that time does get invested.”
Six processes under the microscope
At the Municipality of Wierden, after training employees and MT, six processes were scrutinized: subsidy applications, objections to construction fees, permit applications, complaints and notifications, pupil transport, and the preparation of advisory notes to the Municipal Executive. “To briefly use the process of complaints and notifications as an example, we are very good at taking complaints from citizens, recording them and dealing with them quickly,” said Van den Brink. “What we were not good at was providing feedback to the citizen that their complaint or problem had been resolved. This is only a small addition to the process, but one that makes the citizen more satisfied with our service.” Bos also gives an example, namely the process for student transportation. “Most students need transportation from grade 1 through grade 8. Only when moving or changing schools do things change. However, the Municipality of Wierden approached parents every year. Unnecessary, because there was no reason to do so. So that process could be a lot simpler.”
‘Improvement is something you have to give continuous attention to’
The six processes listed were vetted in Brown Paper sessions by a team consisting of people directly involved in that process and a minimum of two trained process improvers. An MT member also occasionally chimed in, according to Van den Brink, to show commitment, or a consultant from Symbol, to provide guidance. The guiding principle during the sessions: what can be done better, faster and/or more efficiently in this particular process? What steps does the process consist of, who is involved at what point, and where are the bottlenecks? This often produced surprising results. “It created a different way of thinking,” says Van den Brink. “Continuous improvement is a lot of fun, but some people sometimes perceive change as a threat. However, my view is: you don’t have to be sick to get better. Improving is simply something you have to pay continuous attention to, because that’s the only way you can achieve goals together. The emphasis here is on the word “together,” because Lean also promotes cooperation between different departments. A good example is the process of objections against building fees. Practice often shows that citizens who file an objection do not actually object to the amount of the fees but to the issued building permit. By having the Finance Department work together with the Building & Housing Department, the right questions are raised. The Finance Department deals with the objection; the Building & Housing Department is the interlocutor for the content. How such objections are now handled not only affects our operations, but also the quality of our service.”
Engage as many employees as possible
For the Municipality of Wierden, the follow-up process is already visible. Van den Brink: “At the start of the process with Symbol, we mainly looked at processes that made us vulnerable, that had a lot of irritation and/or that involved a lot of money. Now we want to involve as many employees as possible and choose processes where other colleagues can step up. Such as the process of purchasing and procurement. To familiarize the entire organization with Lean, we recently organized a lunch where the results of the first six processes were presented. We have also set up a Lean room, which is purely for sparring with colleagues about processes that can be improved. For example, there is more than enough room to hang the big “brown papers. And to ensure that people continue to be excited about Lean in the future, we are writing a job posting with Symbol for an in-house sparring partner to motivate and encourage people. This is important, because Lean really helps us. It is a tool that we want to continue to use continuously to achieve higher returns. Moreover, it is a tool that I believe every municipality must use, for the simple reason that you owe it to your citizens to reduce costs and continuously improve the quality of your services and operations. With Lean, we as the Municipality of Wierden are working daily to make it more enjoyable and better for our citizens.”
Seize the opportunities: continuous improvement within municipalities
On Thursday, Feb. 8, Symbol is hosting a special event by and for municipalities. This event focuses on continuous improvement in municipalities. Speakers from the municipality of Wierden and municipality of Rijssen-Holten share their experiences. In doing so, you can take a look behind the scenes of the Wierden Municipality.
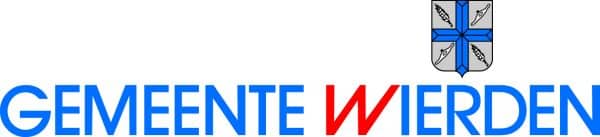