Operational excellence thanks to Six Sigma data analysis: Tata Steel does it
Tata Steel produces, processes and distributes high-quality steel for products that make life easier. It is a company of Dutch origin of which we can be particularly proud. Indeed, it is the sixth largest steel group in the world. Sander van Campen is senior improvement consultant in Tata Steel’s BEX department. “BEX stands for business excellence and has operational excellence as its main goal. To that end, my colleagues and I focus on three pillars, namely daily management, continuous improvement (getting the most out of current processes) and innovation. I focus mainly on continuous improvement. It’s a great sport, because I get to work on problem solving according to the Six Sigma methodology. And that’s also where Symbol comes in.”
Six Sigma projects by Tata Steel Green Belts
Symbol trains Tata Steel employees as Green and Black Belts, assists in project supervision when capacity issues arise and handles certification through the LSSA. “The substantive training is provided by Symbol, we ourselves take on the practical part and the supervision of the projects,” says Van Campen, himself trained by Symbol as a Black Belt. “The projects of these Green Belts are often already quite complex: KPIs are addressed in project teams that do not meet specifications and can be improved quickly. Solving a quality delivery problem for a customer, for example, or having materials available on time for a campaign for a particular product type. Of course, we also work with enabler projects – with environmental and/or safety impact – but in general, we apply the rule that a project must have a positive business case to be allowed to proceed. For certification, a project must generate a minimum annual savings of 20,000 euros. The internal business cases are often higher.”
Data-driven projects
During such projects, the Green and Black belts are coached by Van Campen and his colleagues. “That’s not just to make sure the projects keep running well, but also to help with data analysis. After all, Green Belts get quite a bit to deal with in terms of data analysis. Almost all of our projects are data driven. That is why nowadays we also use advanced analytics, which means that we use advanced models to look at very large data sets. I’m talking about data sets from fifteen variables or more, consisting of at least 100,000 data points. These kinds of data sets are becoming more and more common within Tata Steel.”
Data lake in the cloud
“It’s also one of the reasons our IT organization is working on a data lake in the cloud,” Van Campen continued. “Within Tata Steel there are now a few hundred thousand tables available that contain data. These will soon be neatly centered in one place, in the cloud, so that the data can be found there for everyone. That will be of great benefit to us, because now that data is decentralized and spread out over various systems. Specifically, at the start of a new project, Green Belts have to ask the administrators of the tables for permission. And then they and their project team must also first figure out what data they need, where that data is, and thus which administrator needs to be asked for permission. Cumbersome, especially given the large volume of projects being picked up.”
Projects with Six Sigma data analysis
In recent times alone, there have been a good number of projects in which Six Sigma data analysis has been used. Those projects are woven into the MT’s annual plans and overall objectives, or arise ad hoc. “For example, one project team looked at transporting raw iron to the steel mill. That transport is done in an iron mixer, a kind of torpedo transported by rail, which is then emptied. During the emptying process, some of the iron structurally remained. Since the project, the iron mixer has been emptied more effectively. Per mixer, this produces 1.3 percent more hot metal, yielding more than 200,000 euros annually. But a Six Sigma project has also improved the lead time when feeding a steel coil into the cold strip mill. A time gain of five seconds was achieved. That may not sound like much, but because of the large volume we run, five seconds still means several tens of thousands of euros in savings. In short: Six Sigma projects really deliver a lot to Tata Steel. And more and more data is becoming available and the quality of that data is improving. I am very curious about what the future will bring us.”
Continuous improvement for operational excellence
Of course, it is important that the employees on the project teams are properly trained. And as written earlier, that training is done in part by Symbol. “The trainings are crystallized and of a good level. Very workable too, because we have tatized the training, as we call it. In other words, we worked with Symbol to see how we could translate the general theory into examples within our organization. As a result, the trainings are recognizable for our employees, and the results are very good. This is necessary because our goal is that eventually everyone who has a management role in one of our work units must be at least Green Belt trained. After all, continuous improvement is an important part of operational excellence, and you have to be well trained in order to be able to manage that and apply it in your daily work.”
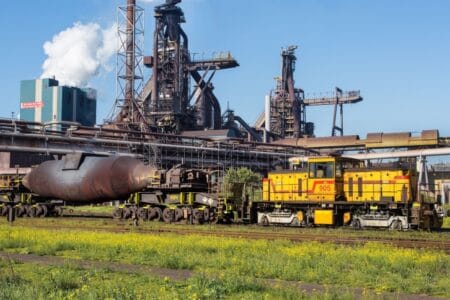
Iron mixers Tata Steel (source: Tata Steel, Internet)
Latest news/blogs
Klarna saved 40 million with AI but lost the trust of its customers
Klarna saved40million with AI but lost the trust of its customersThe question sounds absurd: how...
How do you eat an elephant?
Dutch productivity is falling again - and that offers precisely opportunitiesLabor productivity in...
From Theory to Practice: Junior Consultant at Stoneridge
From theory to practice: Junior Consultant at Stoneridge Before working at Symbol, Junior...