Pento wants to use Lean to “achieve higher quality with less time and budget”
There is a lot of talk in healthcare about Lean. This is often accompanied by terms such as efficiency, effectiveness and working smarter. So is Pento, experts in hearing, speaking and understanding.
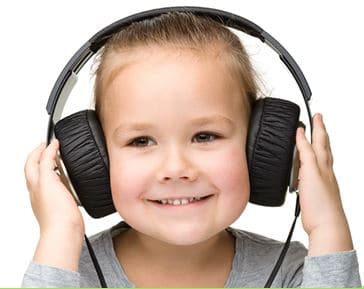
But for them, Lean is more than a set of tools to start working more efficiently. “We want to create a culture where individuals, in whatever position, dare to bring up areas for improvement. A culture where processes are stopped for a moment when someone sees that things can be done better.”
“Pento examines, guides and advises people who have problems with language, speech and/or hearing. We do this from various audiological centers in the North, East and Central Netherlands. People come here for diagnostics, acceptance problems, guidance, rehabilitation, early treatment and advice on hearing aids. At Pento, we use an interdisciplinary approach, in which our employees also collaborate with general practitioners and other medical specialists,” says CEO Jeroen Taalman.
Work smarter
Like many healthcare organizations, Pento is struggling with long wait times and shrinking budgets. “Those waiting times must therefore be shorter, without sacrificing the quality of our care. The conclusion is simple: we need to work smarter and optimize our work processes,” Taalman says. “This is one of the main focal points of the strategic policy plan we wrote in 2015. To this end, we thought about Pento’s right to exist (the why) and its future with all kinds of people from our organization. We then looked for tools that fit us and with which we can achieve that future. Lean Six Sigma has become the tool through which we want to achieve higher quality with less time and budget.”
2016: launch of initial pilot
Together with Symbol, Pento started an initial pilot on site in Zwolle in 2016. Says Taalman, “The team there wanted to reduce the time between a care request coming in and scheduling the first appointment. That seems like an easy task, but nothing could be further from the truth. Much more information than one might expect is needed to arrive at the first appointment. Think about; do we already know this patient, what kind of care need is it and who will do the exam? Together with Symbol, the team mapped out all the steps in the process. We then examined what could be optimized per step and made the right logistical arrangements within the new process about who does what and when. All of this was a time-consuming job.”
Symbol as flying tipper
In phase two, all Pento sites were challenged to engage in Lean Six Sigma. “Very variable issues came out of that,” Taalman knows. “For example, one team wanted to speed up the process around reporting, another team wanted to improve operational management. And yet another team organized their work environment according to the 5S method. The same things are now in the same place in every workroom, so it no longer matters where you work. Symbol guided all the issues – eight in total – and acted as a kind of flying tipper. In the first phase the team was really taken by the hand, in this phase teams were actually activated to get to work themselves. Symbol provided education, organized inspiration sessions, ensured clear planning and monitored progress.”
Lean ‘in the bricks of your buildings’
Taalman indicates that clear results have been achieved in the first two phases. “Quantitative results have been measured very hard by some teams, for example in terms of lead time reduction in scheduling or reporting. Other teams see big improvements, but do not (yet) have statistics to back this up. For me, qualitative results are also important: people are enthusiastic and see that it offers opportunities for subsequent trajectories. That is now the crux. It has to get into the bricks of our buildings, so to speak. In other words: it must become logical to approach processes from the philosophy of Lean. Certainly the shop floor is already bursting with ideas because these people see immediate gains. They just need to be enticed to express those ideas. A culture must be created in which individuals, in whatever position, dare to make improvements. A culture in which processes are stopped for a moment when someone sees that things can be done better. That will work, but we have a long way to go.”
Ambassadors who see opportunities
Therefore, in phase three, Symbol Pento teaches to take charge himself. Symbol wants to make itself redundant. “We don’t want an extensive staff organization for Lean, because then the rest of the organization will sit back. But we do need ambassadors who see opportunities, who make people enthusiastic and who can be questioned. Experts who set concrete goals based on clear measurements and good inventories. That is an important condition for success, otherwise as an organization you quickly fall back into old patterns. Our next step is therefore to train five or six people to become Lean Practitioners via a Belt course. That way we are not vulnerable to turnover in the organization and we can continue to secure knowledge.”
The space to meander
One tip for other (healthcare) organizations Taalman still has. “Lean Six Sigma is a very big topic. Don’t try to fill in the final picture right away, don’t sketch out vistas yet. Don’t deprive your organization of room to meander a bit. Rather, start with one pilot, learn from it and only then take your next step. And don’t forget to involve Symbol from the start. Not only are they very knowledgeable, but they also regularly share literature, workshops and trainings to inspire you. Such a reliable and honourable partner who takes you by the hand is indispensable if you want to deploy Lean successfully.”
Latest news/blogs
Klarna saved 40 million with AI but lost the trust of its customers
Klarna saved40million with AI but lost the trust of its customersThe question sounds absurd: how...
How do you eat an elephant?
Dutch productivity is falling again - and that offers precisely opportunitiesLabor productivity in...
From Theory to Practice: Junior Consultant at Stoneridge
From theory to practice: Junior Consultant at Stoneridge Before working at Symbol, Junior...