Sensata: “We know we deliver quality”
Sensata Technologies Europe develops and manufactures high-quality products with extremely low error rates, especially for Automotive. At the heart of this lies an organization-wide implementation and application of Six Sigma methodology. Good products are not produced by accident. One knows in detail the processes and products and the parameters relevant to quality. With the introduction and application of Six Sigma, the organization has experienced tremendous professional growth.
“We know we deliver quality. That’s not a coincidence.”
Henk Velten
Six Sigma Deployment Leader Sensata
“We have come to realize that we must always continuously deliver top quality and not ‘accidentally good products.’ Therefore, we need to know why our products are good. And that means knowing them. And we do that through this model,” said Henk Velten.
Henk continues: “If you have requirements, you have to translate them into CTQs (Critical to Quality, translation of customer requirements into concrete measurable quality parameters). For this we use FMEA and Design of Experiments, among other things, a method to find the optimal settings of important parameters. We use the Six Sigma toolbox to establish the CTQs and then to ensure that the process itself does not distort the outcome. So we no longer ‘accidentally make good products,’ we know exactly what is important, resulting in an extremely low margin of error.”
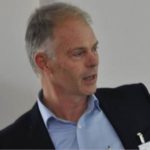
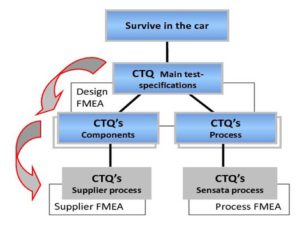
Tips for successfully implementing Six Sigma
“This way of thinking was not readily accepted in the organization. What we needed here was a sense of urgency. I luckily got that because a customer, BMW, once called out that we had to make sure we didn’t come up with ‘Zuvällig gute Produkte’ but with guaranteed good products. That gave the sense of urgency internally to roll out DfSS (Design for Six Sigma) more widely.”
Tips for other organizations on DfSS? Henk lists, “To begin with, provide top down support to support bottom up initiatives. A clear sense of urgency is also needed. Communicate three times as much as you think is necessary, including success stories. Further, provide an internal coordinator or deployment leader. Last but not least, use outside expertise.”