DMAIC
The DMAIC roadmap is used to improve, optimize and stabilize business processes and products. DMAIC stands for a structured and standardized approach to a problem. The roadmap is driven by making decisions based on data and facts.
DMAIC is an abbreviation for Define, Measure, Analyze, Improve and Control
DMAIC is an abbreviation for Define, Measure, Analyze, Improve and Control. This roadmap is used for Six Sigma projects (CIMM level-IV). For Lean projects (CIMM level-III), either the PDCA or the DMAIC roadmap can be used. For Kaizen projects (CIMM – level-II), it is recommended to follow the PDCA roadmap because it is simpler.
The Define phase of the roadmap defines the operational problem, establishes a Project Charter and defines the Critical to Quality (CTQ) parameter. In the Measure phase, the measurement system to measure the CTQ is validated. The Analyze phase analyzes the current process and identifies potential factors affecting the measured value. In the Improve phase, improvements are defined, implemented and verified. Finally, in the Control phase, measures are taken to secure the improvements. We will explore each of these phases in more detail below.
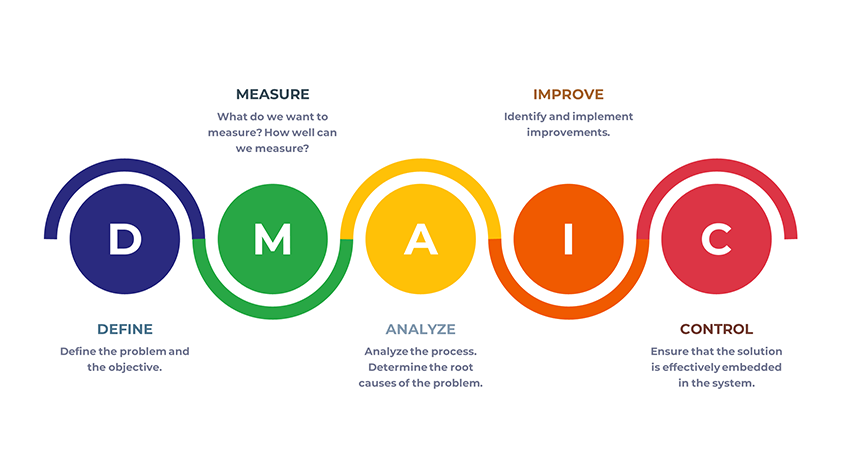
Sometimes you see project selection mentioned in the Define phase, but formally project selection is not part of the DMAIC roadmap and project selection takes place before that. The Champion selects a project based on criteria such as size, impact and urgency. However, it may be that during the evaluation in the early stages of the DMAIC, the scope or team will be changed. Sometimes a quick DMA is done prior to the actual start of a full DMAIC. Portfolio management and project prioritization are also not part of the DMAIC roadmap, but are managed at a higher level by the Champion or by the Master Black Belt.
DMAIC – Define:
Every Lean Six Sigma project begins with the Define phase. Originally, this phase did not exist, but General Electric added the Define phase to the original MAIC methodology. Based on the problem definition and scope of the project, a team is assembled and a project manager appointed. The Champion is the problem owner and principal of the project.
The purpose of the Define phase is to clearly define the problem definition, objective, scope and an initial estimate of the duration of the project. A Project Charter will be prepared at the beginning of the project that includes all of these components. The Define phase also helps clarify why the problem is actually a problem and how big a problem it is. This is expressed as an amount. This is important as time and money are invested in the project.
The description of the problem is done from the point of view of the external customer (Voice of Customer) and/or from the point of view of the organization (Voice of Business). The Define phase determines which measurable quantity can be linked to the customer’s problem. This so-called Critical to Quality (CTQ) is the common thread throughout the DMAIC project. Each Lean Six Sigma project focuses on a limited number of CTQs. To establish the CTQs, a CTQ Flowdown is prepared. For Lean projects, the CTQ is often related to numbers or time (lead time, delivery time, processing time, utilization rate, etc).
DMAIC – Measure:
The Measure phase determines the measurement procedure and how well the measurement system is capable of measuring the CTQs. It is important for the team to ensure that the measurement system, and the data collected with it, is valid and reliable before proceeding to analyze this data. To make a statement about this, a Measurement System Analysis or Measurement System Analysis (MSA) is performed on the measurement system. The Measure phase is often seen as the most difficult phase of a DMAIC project, because data are sometimes not yet present and performing an MSA is difficult. For Lean projects, it is very important to clearly define the definitions of the CTQ and the source for the data so that there is no discussion about performance.
Also, within the Measure phase, the difference between current performance (Baseline performance) and desired performance (Target performance) is determined. This applies to both Lean and Six Sigma projects.
DMAIC – Analyze:
The goal of any Six Sigma project is to get the CTQ on target and reduce the variation of the CTQ. The purpose of the Analyze phase is to identify, validate and determine factors that influence variation. These factors must be adjusted or eliminated.
This phase establishes the relationships between the CTQ (also called Key Process Output variables, response or ‘Y’) and the Key Process Input variables (also called ‘X’-s). Often a large number of potential influencing factors are identified at the beginning through, for example, a brainstorming analysis. The number of potential influence factors is then reduced by conducting screening experiments. A hypothesis is then determined and experiments are conducted to investigate the hypothesis. The result is a (mathematical) model showing the relationships between the influence factors (X1..n) and the CTQ. Analysis tools, such as Hypothesis Testing or Design of Experiments (DOE), can be used in this phase. Within Lean projects at this stage, a “Value Stream Map – Current State” or “Spaghetti Diagram” of the current situation is often created to depict waste and determine opportunities for improvement.
DMAIC – Improve:
The goal of the Improve phase is to implement and verify the solution to the problem. To determine the optimal setting for a process, certain techniques can be used such as regression analysis or Design of Experiments. Within Six Sigma projects, a “Process Capability Analysis” is often created to examine the performance of the improved process.
Within Lean projects at this stage, a “Value Stream Map – Future State” will often be created showing the desired or future state. This could be a modified process or a new layout of the production line. The Future State also identifies the improvement projects that must be carried out to achieve the new situation. In the Improve phase, TPM or Kaizen projects are implemented to eliminate waste or correct quality problems.
DMAIC – Control:
The purpose of the Control phase is to secure the results achieved in the organization. Even though the problem has already been solved, the team should remember to take this phase seriously and prevent the problem from reoccurring. The best way to achieve this is to secure improvement with “Poka Yoke” solutions, which are not dependent on the employee. This is not always possible, and then the solution still depends on the employee’s method followed. This is especially true if the solution results in a different way of working. Options for securing improvement in this case include creating new work instructions, providing training, and modifying quality documents such as the PFMEA and the “Control Plan.
In the Control phase, the savings of the project are also determined and compared to the target savings as determined at the beginning of the project. Then the assignment is formally returned to the client, the Champion. After all, the job of the Champion or department manager is to appreciate the team for its performance.
In addition to the DMAIC roadmap, some organizations apply an additional step, the Replication phase. The purpose of the Replication phase is to identify other products or processes that may benefit from the result achieved. Replicating the improvements and sharing the “Lessons Learned” help gain buy-in for future DMAIC projects.
DMAIC 14-step roadmap
The five DMAIC phases are followed by all Lean Six Sigma Belts in the world. Because the five stages are very comprehensive, they are divided into a number of steps. Several variations exist for this detailing. The Table below shows an example of the 14-step roadmap used by the LSSA (Source: Minitab Quality Companion).
DMAIC roadmap
Define | 1. Define project and establish delineation |
2. Define what is wrong (defective) and determine CTQs | |
3. Plan and document the project | |
Measure | 4. Evaluate the measurement system |
5. Determine the current performance of Y | |
6. Set improvement goals | |
Analyze | 7. Map the process and inputs. |
8. Determine factors of influence(X1..n). | |
9. Determine Y = f(Xi) | |
Improve | 10. Determine the optimal process setting |
11. Implement the proposed improvement | |
12. Validate the improvement introduced | |
Control | 13. Secure the improvement |
14. Close the project |
How do you apply DMAIC?
Want to learn for yourself how to tackle projects via the DMAIC roadmap? Then follow our Lean Six Sigma Green Belt training or Lean Six Sigma Black Belt training! Both trainings can also be delivered in-company!