Concrete results at Peka Kroef after Lean (Six Sigma) Green Belt training from Symbol
Do you ever think about where the prepackaged potato slices in the supermarket come from? After reading this reference, you’ll know: from the Peka Kroef factory in Odiliapeel.
This family-owned business has specialized in processing fresh, chilled potato products since 1970. Symbol recently provided Lean (Six Sigma) training for 10 employees of this company.
And the results are too good not to share.
Lean training from Symbol
“We had already set up an improvement team ourselves to solve some challenges in our plant. That team delivered great results, but the team members still lacked knowledge of Lean methodologies. That’s why I approached Symbol for Lean training, specifically the Lean (Six Sigma) Green Belt,” says Geert van Dooren, Manager of Operations at Peka Kroef. “Niels Heuthorst, Business Development Manager at Symbol, then came up with the suggestion to organize the training more broadly than just for the members of the improvement team. After all, if you want to improve continuously, the whole organization has to go along with it. So we approached several people, and so a group of 10 enthusiasts emerged who attended the training.”
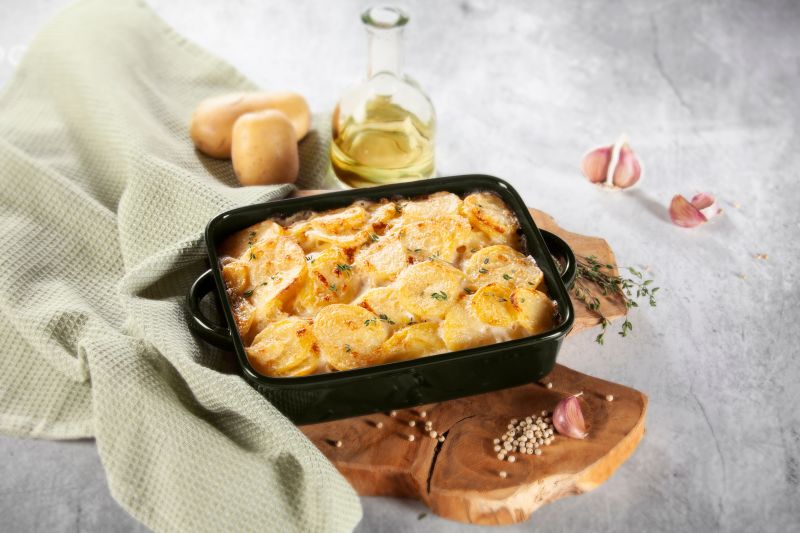
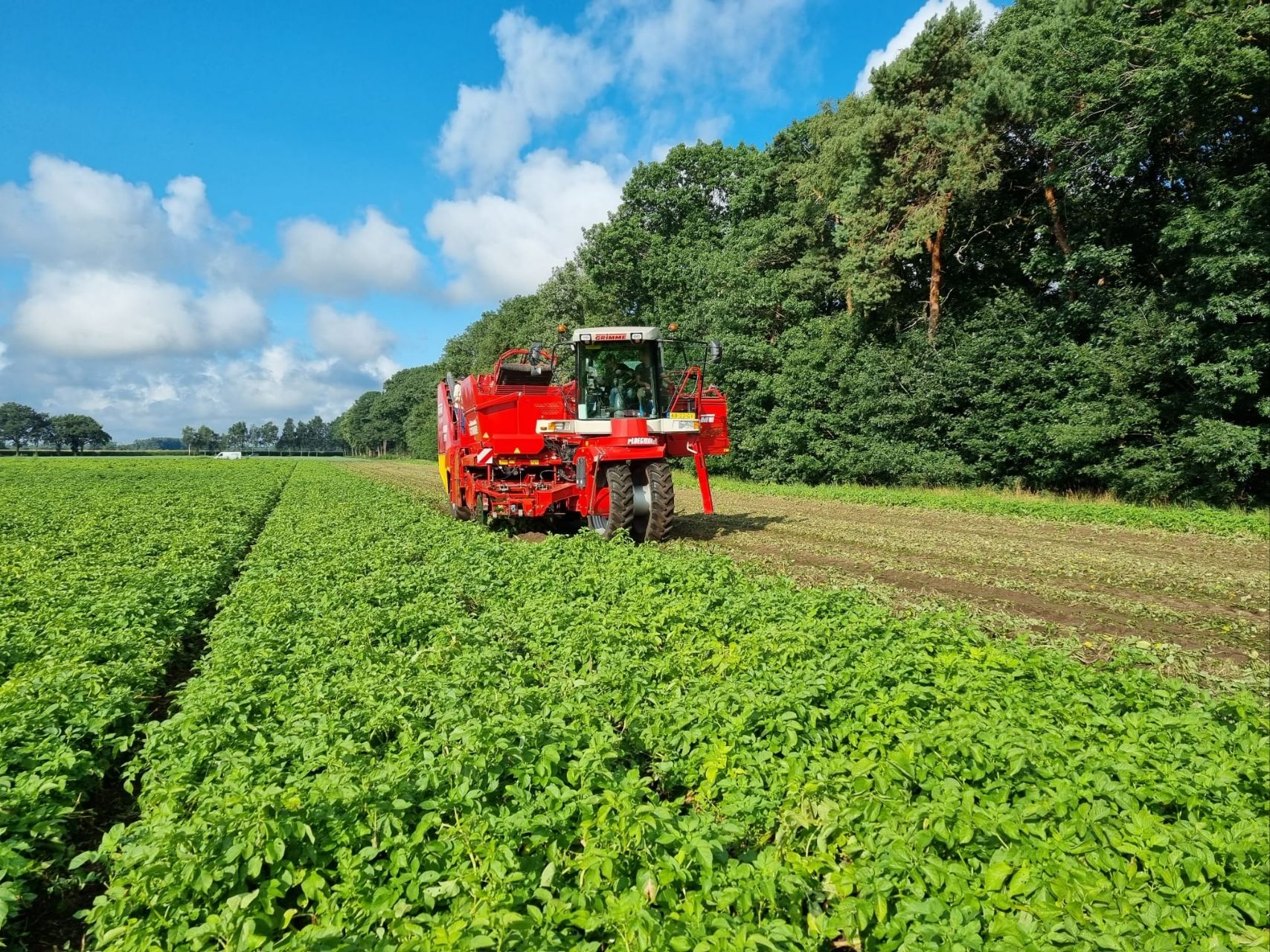
Lean Six Sigma training: an opportunity
Prior to the training, Geert conducted an intake with all participants. “I wanted to tell them more about the training, but also about the expectation from the organization. In fact, we offered everyone the opportunity to go for Lean Six Sigma, but it was not a requirement. If someone just wanted to master Lean techniques, that was fine too.” Symbol consultant and trainer Arnold Verhagen adds: “What I liked was that everyone at the start had the drive to go for Six Sigma – even though it might be difficult. By combining theory and direct application in one’s own practice, I have tried to make it as practical as possible. Prior to the first day of training, for example, participants were instructed to come up with their own topic and bring it to the training. We also did many games and exercises.
In the end, a few participants chose to do Lean Six Sigma and a few others completed only Lean. And most of them now have their certificates under their belt.”
Furthermore, doing the Lean training with people from different departments – from QA to production – was a hit. They got off their little island that way, which now ensures that they know each other better.
Incompany training Lean Green Belt
Both the participants and Geert experienced the training as very positive. “Because the Green Belt training was in-company, we were able to dive right into our own issues. Participants also learned techniques that help them work smarter, such as 5S and working with day starters. We are going to roll out these kinds of techniques in the near future. And after the training Arnold also coached the participants individually – very valuable. “Think of it as a doctor’s office,” Arnold says. “In a 1-on-1 meeting, participants were able to ask me questions and share their thoughts on their improvement projects. I spent a total of 10 days on location for this. Not everyone used the “consultation hours” equally, but a number of people were able to go that extra mile because of it.
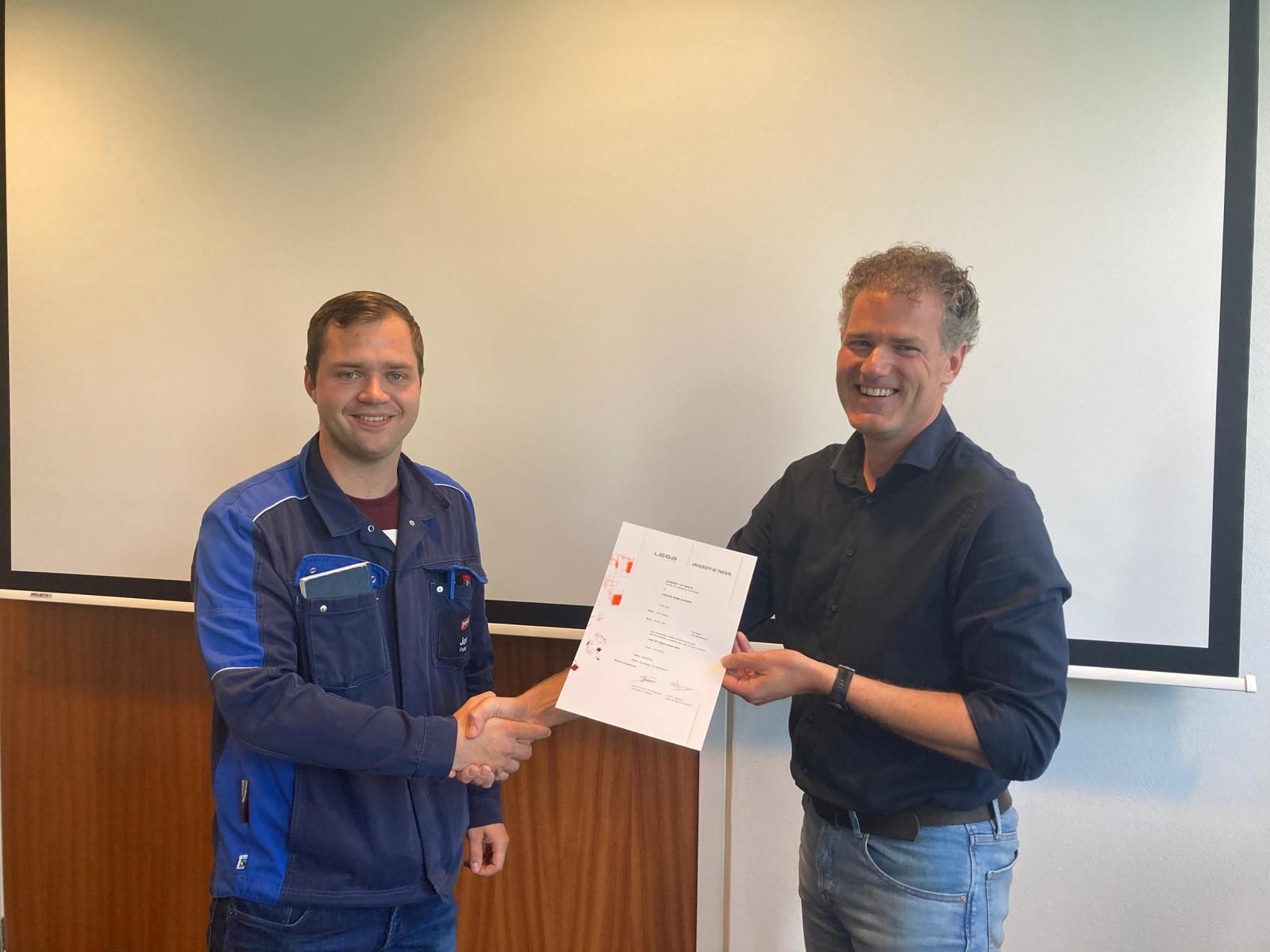
Improvement project with a concrete result
Geert: “Furthermore, it was a big hit to do the Lean training with people from different departments – from QA to production. This got them off their little islands, which means they now know how to find each other better. So internal communication has improved – a nice side result. But the training also produced very concrete results. For example, one participant set up a cross-departmental project team to reduce the water consumption of our high-pressure plant. Thanks to the different perspectives and insights, the three of them arrived at a good solution in this improvement project. And meanwhile, water consumption has dropped significantly.”
Business-driven continuous improvement
In the meantime, Geert himself attended the one-day Champion & (Lean) Leadership training at Symbol. “As a result, we are now more business-driven with continuous improvement. Namely, I look at which improvement projects fit the organizational goals. For example, reducing the water use of the high-pressure plant fits with our goal of reducing our water consumption per ton. Near that objective, by the way, a second improvement project was successfully completed. In fact, a training participant scrutinized a machine that suddenly consumed more water than before. He used various Lean methodologies to map out the machine’s process to examine exactly where in the machine and under what conditions more water is consumed. Again, water consumption is now significantly reduced.
Ambassadors of continuous improvement
Another concrete result was achieved in an improvement project that examined the number of kilograms produced per man-hour. “Production was too low,” Geert says. “Thanks to the application of various Lean techniques, more kilograms are now produced per man-hour. Results like this matter!” Arnold adds: “And a few more improvement projects are currently underway. For example, someone is working on reducing the changeover time from one packaging to another and another is working on getting a more accurate weight for the bags. A good learning point for the MT in this process was that it pays off to give people the freedom to do their own work. Previously, the MT managed employees top-down. Now people feel ownership: they themselves are more allowed to think about how they can contribute to the organization’s objectives, such as increasing efficiency or reducing the number of failures. As a result Peka Kroef now has real ambassadors of continuous improvement in house.”
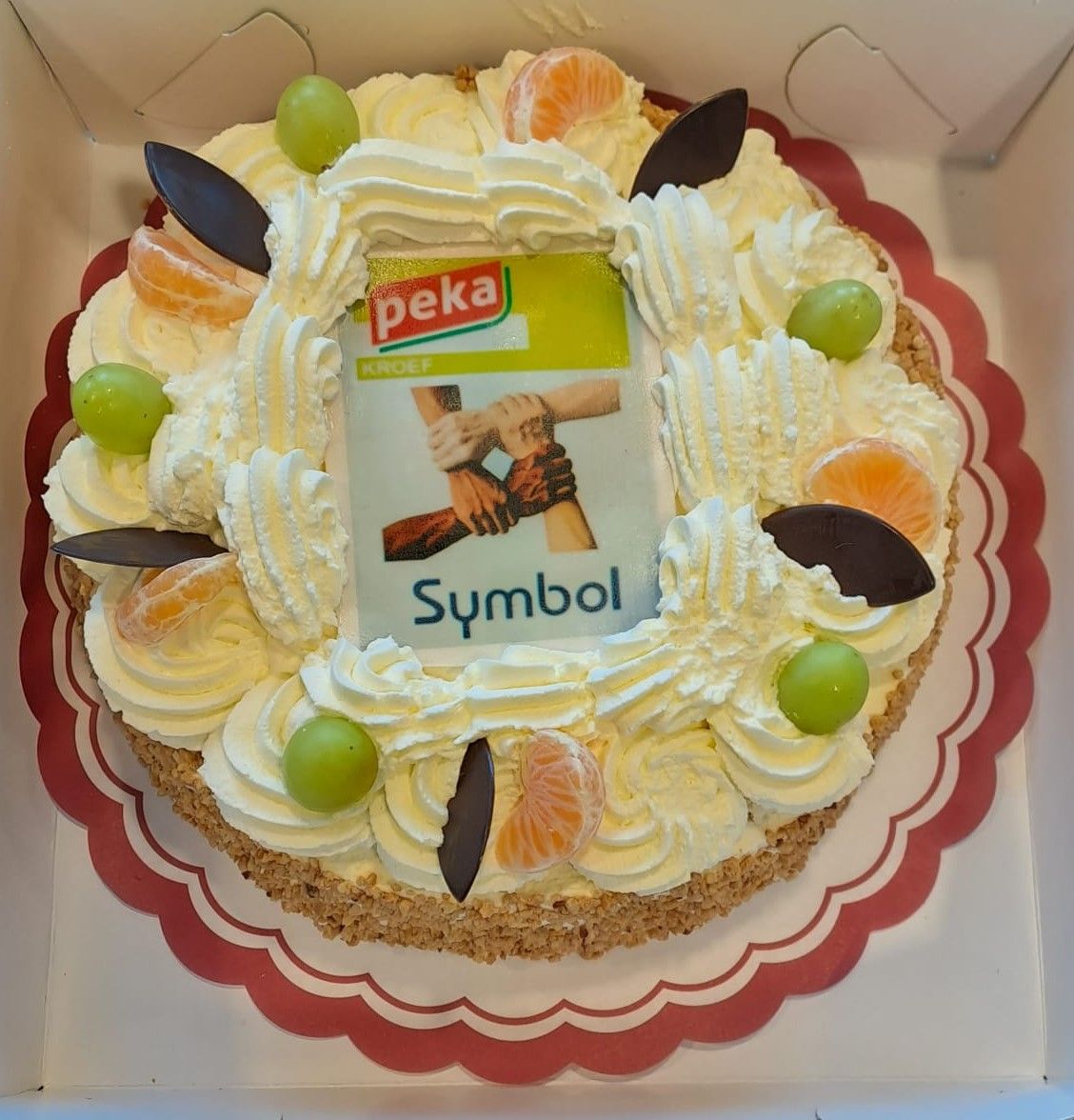
Looking for inspiration and improvement?
Want to learn more about Symbol’s project approach? Then contact us at 053 – 20 30 240 or using the form below. Do you want to train yourself in process optimization? Then check out our Lean Green Belt and Lean Black Belt training courses!