DMN-WESTINGHOUSE: Hoe kun je slimmer werken, daar gaat het om!
Johan Meima is in 2011 bij DMN-WESTINGHOUSE in dienst getreden als Quality manager. Er lag een grote uitdaging. DMN-WESTINGHOUSE was een productiebedrijf van de oude stempel, met focus op productie. Hetgeen natuurlijk prima is, maar wat vooral een buitenstaander opviel is dat het er binnen nogal somber uitzag. Tegenwoordig is het ook in de productie schoon en licht, prettig om te werken. “Daarmee zijn we dus begonnen. Een grote schoonmaakactie”, aldus Johan.
DMN-WESTINGHOUSE ontwikkelt en produceert al ruim 40 jaar doseersluizen, wisselkleppen en andere, verwante componenten voor de stortgoedindustrie. DMN-WESTINGHOUSE biedt wereldwijd maatwerk in componenten voor de voedings-, dairy, plastic-, (petro) chemische, farmaceutische, mineralen-, energie en biomassa industrieën. Sinds de oprichting in 1950 is DMN-WESTINGHOUSE een productiebedrijf geweest. Tegenwoordig worden de doseersluizen en wisselkleppen machinaal bewerkt en geassembleerd in eigen productiebedrijven in Nederland, USA en Duitsland. Het hooggekwalificeerde personeel en zeer geavanceerde machinepark stelt DMN-WESTINGHOUSE in staat hoge kwaliteitscomponenten met gedetailleerde afwerkingen en nauwkeurige spelingen te maken.
“Hoe kun je slimmer werken, daar gaat het om!”
Johan: “Ons proces is opgedeeld in drie ‘Gates’. ‘Gate 1’ wil zeggen het moment van (telefonische) ontvangst van de order tot en met de bevestiging en het afgeven van levertijd. ‘Gate 2’ is het samenbrengen van de diverse productonderdelen voor assemblage. Dus de inkoop van materialen en eigen productie. ‘Gate 3’ tenslotte is het assembleren van het product. Alle materialen zijn aanwezig. Het product wordt in elkaar gezet en klaar gemaakt voor verzending.
Als eerste inzicht in je processen hebben
Als eerste hebben we Gate 1 aangepakt door middel van Value Stream Mapping. We zijn van 16 dagen doorlooptijd naar 2 tot 3 dagen doorlooptijd gegaan. En in onze laatste benadering gaan we zelfs naar 0 dagen doordat we nagenoeg direct al een levertijd aan de klant kunnen afgeven, bij het plaatsen van de order.
In Gate 2 zitten we nu op 11 dagen. De volgende stap is het verbeteren van de ‘flow’. Dat wil zeggen dat we willen dat de diverse onderdelen soepel door het proces lopen, zonder stagnaties, tussenvoorraden of juist tekorten en precies aansluitend bij de klantvraag. Begin 2017 gaan we dit proces aanpakken, met als doel een verdere verkorting van de doorlooptijd.
Het verbetertraject op de doorlooptijden van Gate 3 loopt nog. We zitten nu in een verbouwing. Het proces duurt nu ongeveer 4 dagen. We gaan echter eerst de productie-omgeving verder opknappen en opnieuw inrichten. Dat levert niet direct financieel iets op, maar wel een betere en overzichtelijker werkplek. Daarna gaan we kijken hoe we slimmer kunnen werken.
58 Verbeterideeën na een Yellow Belt training voor iedereen…
Eind 2014 ontstond de discussie of het verbeteren aan de hand van de Lean filosofie en principes wel de juiste weg was. Met het personeel en de directie hebben we daarom in 2015 een bezoek gebracht aan Scania. Dat gaf de doorslag om verder te gaan. We hebben Symbol gevraagd om iedereen van de telefoniste tot en met de directie een Yellow Belt training te geven, zodat we allemaal dezelfde taal spreken en mee kunnen doen en denken. Vervolgens hebben we de medewerkers uitgenodigd om hun verbeterideeën in te dienen. Hieruit kwamen in de cursus direct 58 suggesties voort, bijvoorbeeld het digitaliseren van het archief, herinrichten van de verkoopafdeling, herinrichten van de zaagafdeling, invoering van nieuwe magazijnstellingen met een duidelijk voorraadbeheersysteem, vereenvoudigingen van het product en de invoering van handscanners. Het streven is om maximaal 5 projecten tegelijkertijd aan te pakken en ook een aantal ‘microprojecten’, kleine projecten waarmee snel resultaat behaald kan worden.
Veranderingen doorvoeren vergt een lange adem
We hadden zeker te maken met weerstand. Veranderen is een moeilijk traject. Wij gaan hiermee om door zaken bespreekbaar te maken, mensen op te leiden. Het is heel belangrijk om iedereen erbij te betrekken. En om support te hebben vanuit het management. Maar soms moet je toch gewoon doen. Stappen maken, zodat gelijk hebben en gelijk krijgen bij elkaar kunnen komen. Maar het is een lang traject, waarin vasthoudendheid en doorzettingsvermogen noodzakelijke eigenschappen zijn. Bij ons is het de verwachting dat het zo’n 7 jaar duurt. Nu kunnen we wel stellen dat het continu verbeteren bij iedereen tussen de oren zit en we willen dat dit beklijft.
We hebben een groei doorgemaakt. Iedereen moet gaan inzien dat er genoeg mogelijkheden zijn tot verbetering en dat dit wat oplevert. De rol van de trainer van Symbol was hierbij erg belangrijk. In de trainingen en ook daarbuiten werd samengewerkt met collega’s waarmee voorheen nooit contact was. Dit werd als erg inspirerend ervaren. Uiteindelijk wil men zien dat alle inspanningen en veranderingen ook wat oplevert.
In de Yellow Belt trainingen zijn projectteams opgericht, samengesteld uit betrokken medewerkers. De Yellow Belt is een brede training, waaruit mensen in ieder geval veel ideeën meenemen. Iedereen krijgt de kans om deze ideeën in projectteams ook tot uitvoering te brengen. De samenwerking in teams is hopelijk blijvend. Je moet de mensen ook een kans geven om veranderingen mee te maken.
Intern hebben we nu twee Green Belts en twee Black Belts. Het alloceren van tijd voor hun verbeterprojecten is lastig. Door tijd ervoor te maken hopen we ook creativiteit los te maken. Per 1 juli hebben iemand in een functie die 40% van zijn tijd mag gaan besteden aan Lean Six Sigma verbeterprojecten. Dat is weer een stap!
De hele transformatie heeft zeker invloed op de sfeer gehad. De ruimtes zijn schoner en lichter. Mensen zien dat er wat gebeurt. Dit wil niet zeggen dat mensen het er altijd over eens zijn dat dit de verdienste is van het nieuwe ‘Lean’ denken.
Bewustwording creëren
Wat ik nu anders gedaan zou hebben? Ik ben te gemakkelijk aan de slag gegaan, zonder de directie echt mee te nemen of mee te krijgen. Hun actieve rol is van cruciaal belang in het al dan niet slagen van een Lean implementatie. Vorige maand hebben we alsnog een sessie met de directie georganiseerd om hierover te praten. De directie moet zichtbaar zijn, voor de mensen staan. Niemand had het over klantgerichtheid, leiderschap tonen, voorwaarden, etc. Sinds we de masterclass met het management hebben gedaan, is dit bewustzijn er wel. Het management heeft echt een belangrijke rol hierin. Daarbij hadden we geen ‘sense of urgency’. Die hebben we ook niet gekozen. Dus of we wel of niet veranderingen zouden doorvoeren, er zou niet direct bloed uitstromen. ‘Achterblijven in de markt’ werd hier wel genoemd. Maar mensen moeten dat ook zo voelen. De markt is inderdaad aan het veranderen. Klanten zijn ineens heel groot. En je hebt in toenemende mate te maken met regelgeving uit Europa. Nu lopen we in onze branche voorzichtig voorop. We kunnen goed aanhaken, niet in de laatste plaats doordat we een zetel hebben in de werkgroep bij FME die onder andere ook meepraat over de Europese wet- en regelgeving.
Tips voor andere organisaties? Creëer een ‘sense of urgency’. Lees bijvoorbeeld het boek ‘Onze ijsberg smelt’ van John Kotter. Dat is een mooie start om bewustwording te creëren. En, zoals gezegd, directie en management in de frontlinie is een absolute voorwaarde om succesvol te zijn. Zij moeten zich duidelijk uitspreken met betrekking tot thema’s als ‘wat is échte klanttevredenheid?’ Is dat je eigen portemonnee of is het wat de klant vraagt? Vervolgens moet je dit vertalen naar je proces, slim vertalen. Betrek de hele organisatie erbij en leidt de mensen op!
We zijn er trots op dat onze mensen het nu zo goed oppakken. Ik heb er veel vertrouwen in. In de techniek willen mensen ook graag verder. Iedere avond vraag ik mij verwachtingsvol af wat er morgen weer beter gaat. Ik wil graag mensen inspireren om te verbeteren en maar ook dat ze daarbij zichzelf kunnen zijn in hun werk. Verbeteren in hun team, als organisatie, maar ook in hun eigen procesjes. Hoe kun je slimmer werken. Daar gaat het om!”
Johan Meima heeft Dick Theisens, CEO van Symbol BV, ontmoet tijdens een bijeenkomst van LSSN (Lean Six Sigma Nederland). Het feit dat Symbol naast consultancy en coaching gedegen opleidingen biedt en examineert volgens LSSA richtlijnen hetgeen een internationaal erkend diploma oplevert, was een belangrijke motivatie om voor Symbol te kiezen.
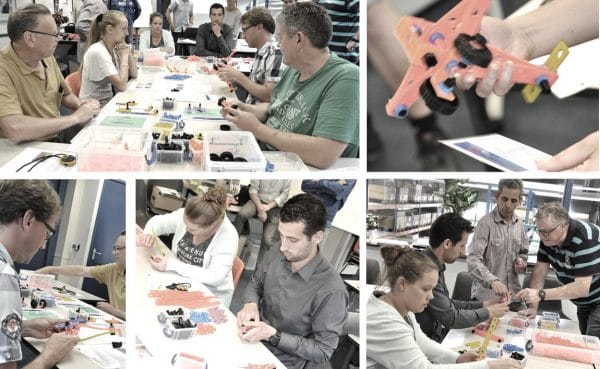
Laatste nieuws/blogs
AI bespaarde 40 miljoen Maar wat gebeurde er met het vertrouwen?
Klarna bespaarde miljoenen met AI door 700 medewerkers te vervangen maar verloor het vertrouwen van klanten. Deze casus laat zien waarom AI niet alleen een technologische keuze is, maar ook een strategische.
Hoe eet je een olifant?
Grote verbeteringen beginnen klein. Deze blog laat zien hoe je complexe veranderingen stap voor stap aanpakt met structuur, gedragsverandering en focus op wat écht waarde toevoegt. Geen oppervlakkige tips, maar concrete inzichten waarmee je vandaag al kunt starten.
Nederlandse productiviteit daalt opnieuw – en dat biedt juist kansen
De arbeidsproductiviteit in Nederland is opnieuw gedaald. Maar achter deze cijfers schuilt ook een kans: voor organisaties die bereid zijn slimmer te werken. In deze blog lees je welke structurele verbeteringen écht effect hebben – en waarom AI, rust en focus daarbij onmisbaar zijn.